A Basic Introduction to Kelly Bars for Drilling Rigs
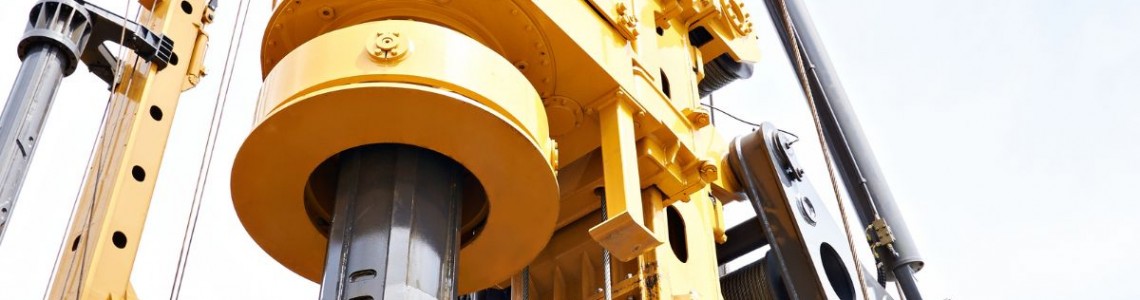
Kelly bars play a crucial role in the operation of drilling rigs. Whether it's foundational drilling, construction, or mining applications, these essential pieces of equipment make the drilling process highly efficient. We’ll provide a basic introduction to Kelly bars for drilling rigs and explore their purpose, the types, and other essential information.
Understanding a Kelly Bar
A Kelly bar is a long, telescopic tubular structure attached to a drilling rig's rotary table. It transfers drilling torque from the rig's power unit to the drilling tool. This connection is integral for any drilling operation, as it enables the drilling operators to maintain a consistent level of force and stability for the project.
Kelly bars are the backbones of drilling. They come in various lengths, diameters, and configurations to accommodate different drilling depths, soil compositions, and rig capacities. Selecting an appropriate Kelly bar is crucial for a successful drilling operation.
Types of Kelly Bars and Their Applications
We can classify Kelly bars into several types based on their design and the drilling requirements they cater to. Understanding the types of Kelly bars can help you select the best one for your drilling operation.
Friction Kelly Bars
These bars transmit torque through the friction between the inner and outer sections. They are ideal for soil layer drilling and are known for their versatility. You would use friction Kelly bars in deep excavation projects where you must drill through multiple soil layers.
Locking Kelly Bars
As the name suggests, these bars utilize a mechanical lock to transfer torque, which makes them suitable for drilling through dense substances like rocks. Locking Kelly bars are designed for high torque operations, ensuring stability and efficiency while drilling.
Combined Kelly Bars
These bars combine the features of friction and locking Kelly bars. They offer versatility in drilling operations, and you can adjust them according to the conditions of the work site. For instance, you can switch a combined Kelly bar to friction mode for soil layer drilling and to locking mode when encountering hard layers of rock.
The Benefits of Using Kelly Bars in Drilling Operations
Kelly bars contribute to the efficiency, safety, and success of drilling operations. One major advantage of utilizing a Kelly bar include its adaptability to different drilling conditions. This comes in handy when drilling through varying soil compositions or when you must drill at great depths.
By delivering powerful torque transmission, Kelly bars ensure the drilling tool can penetrate dense geological formations, making them essential for drilling operations in environments where durable equipment is necessary. Additionally, Kelly bars are designed for quick disassembly and easy transportation. This feature greatly reduces the setup time across drilling sites, enhancing the productivity of your drilling operations.
Using Kelly bars in drilling significantly enhances the effectiveness of your operations and leads to a successful and safe drilling process.
Tips for Successfully Setting Up a Kelly Bar
Consider factors such as the drilling rig's capacity, the characteristics of the geography, and the desired drilling depth in order to set up a Kelly bar successfully. Here are some practical tips to assist you in setting up a Kelly bar:
Understand the Geological Conditions
Thoroughly analyze soil composition, rock hardness, and water content before setting up your Kelly bar. This will help you choose the right Kelly bar type and extension for the job.
Match the Kelly Bar With the Drilling Rig
Ensure the Kelly bar is compatible with your drilling rig's power unit, size, and function. An incompatible setup could lead to operational inefficiencies or even damage to the equipment.
Use Kelly Bar Extensions When Needed
Use Kelly bar extensions if the project requires deep drilling. These extensions can help your rig reach the necessary depth without compromising operator safety.
Secure the Connection
Secure the Kelly bar to the rotary table to ensure torque transmission during drilling.
Perform Regular Maintenance
Regularly maintain and inspect your Kelly bar to keep it in optimal working condition. This includes checking for signs of wear and tear, cleaning the component, and lubricating the bar as needed.
Remember, correct setup and regular maintenance can significantly improve the success of your drilling operations.
Common Issues With Kelly Bars and How To Avoid Them
While Kelly bars are essential for drilling operations, several issues can impact their performance and longevity, which can lead to delays in drilling or even compromise the safety of the workers on-site. Here are some common issues and tips for avoiding them:
Wear and Tear
Constant use of Kelly bars, especially in harsh drilling conditions, can wear them down. Perform regular inspections and maintenance, and replace worn-out sections to avoid this issue.
Incorrect Setup
An incorrectly set up Kelly bar can lead to inefficiencies in drilling or damage to the drilling rig. Follow the tips in this guide for a successful setup.
Insufficient Depth
If the drilling depth exceeds the length of the Kelly bar, it can lead to drilling inefficiencies. Use Kelly bar extensions to reach the desired depth without compromising the operation's safety.
Inadequate Torque Transmission
This problem can occur if the Kelly bar does not align with the rotary table or if there is an issue with the drilling rig's power unit. Regular checks and maintenance can help you avoid this problem.
Improper Use in Varying Geological Conditions
Using the wrong type of Kelly bar for your geological conditions can lead to inefficiencies and damage. Understand your site’s geological conditions before choosing a Kelly bar, and consider using combined Kelly bars for varied conditions.
Anticipating and addressing these common issues can significantly improve the success and safety of your drilling operations. Regular maintenance, correct setup, and understanding the geological conditions are key to maximizing the lifespan of your Kelly bars.
With this basic introduction to Kelly bars for drilling rigs, you can make an informed decision about Kelly bars for your drilling operations. Then, you’ll be able to get the job done safely and efficiently. Revisit this guide whenever you need to ensure you’re making the best decisions for your drilling projects.