An Introduction to Geotechnical Drilling Techniques
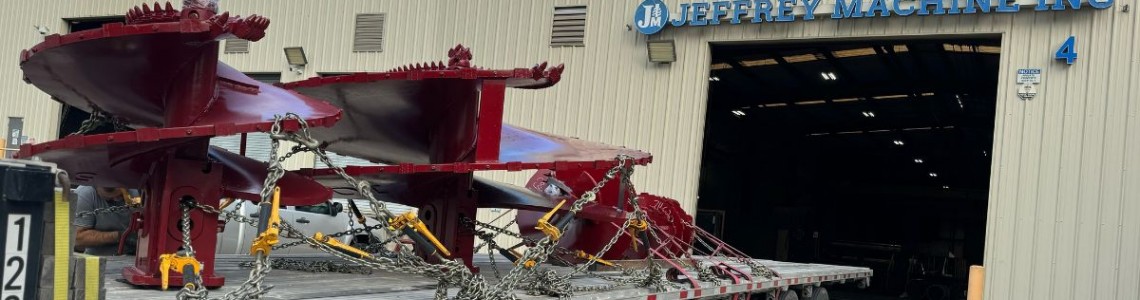
Geotechnical drilling is daunting work in the construction, foundation engineering, and earthwork sectors. It helps professionals in these fields understand soil conditions, which directly impact the stability and longevity of any structure.
Engineers must know the key techniques for geotechnical drilling, how they work, and why they matter. Whether you’re new to foundation drilling or looking to enhance your knowledge, this introduction to geotechnical drilling techniques will help you plan successful projects.
Common Geotechnical Drilling Techniques
Several methods are used for geotechnical drilling, and each works best in specific environments and with certain materials. Selecting the right method depends on soil conditions, depth requirements, and project goals. Here are some of the most common techniques:
Auger Drilling
Engineers frequently use auger drilling techniques for soil sampling and shallow subsurface investigation. This method uses a helical drill bit, called an auger, which rotates into the ground to remove soil and create a borehole.
Engineers rely on auger drilling for environmental assessments, foundation investigations, and exploratory drilling up to moderate depths. The auger drilling method is particularly effective in soft to medium soils, such as clay, silt, and loose sand.
Auger drilling is fast and cost-effective, making it a popular choice for many construction projects. It provides high-quality samples without disturbing the soil layers. These drills are also easy to transport and set up, making them ideal for small- and medium-scale projects.
Heavy-duty augers are suitable for more difficult surfaces and environments. They offer enhanced durability and efficiency while tackling challenging conditions like dense clay and rocky terrain.
Rotary Drilling
Rotary drilling uses a rotating drill bit that grinds through soil and rock to reach deeper subsurface layers. It is often paired with a fluid system that pumps water or mud into the borehole to stabilize it and flush out debris. This fluid also helps cool the drill bit, preventing overheating and excessive wear and tear.
Rotary drilling is versatile and works in various conditions, from loose sand to hard rock. Engineers often use this option for deeper investigations, such as those needed for large infrastructure projects, skyscrapers, and bridges. Its depth and precision suit projects that require a detailed understanding of underground conditions.
There are two main types of rotary drilling. Air rotary is ideal for dry, rocky environments where mud or water may not be necessary. Mud rotary is useful when the soil is soft or prone to collapse, as the mud stabilizes the borehole.
Percussion Drilling
Percussion drilling is ideal for breaking through tough rock and dense materials. With this method, a heavy hammer repeatedly strikes the drill bit, pulverizing the material beneath it.
Percussion drilling offers excellent performance in hard, consolidated soils or rock formations. It is slower than rotary drilling but is often the only solution in extremely dense layers. It’s commonly used in mineral exploration and when drilling through bedrock for foundation construction.
Sonic Drilling
No introduction to geotechnical drilling techniques is complete without mentioning sonic drilling. This highly efficient and precise technique uses high-frequency vibrations to reduce friction at the drill bit.
It allows the drill to penetrate various materials quickly and with minimal resistance. The vibrations cause the surrounding material to fluidize momentarily, allowing the drill to move forward without rotating or hammering.
One key advantage of sonic drilling is its ability to produce continuous, undisturbed core samples. Engineers favor this method for environmental studies, geothermal drilling, and sensitive sites where minimizing ground disturbance is important.
Sonic drilling is useful in various ground conditions, from loose, unconsolidated soils to dense rock formations. It also works well in mixed soil environments where other methods may struggle.
Direct Push Drilling
Direct push drilling, also known as probe or drive drilling, involves pushing or driving a tool into the ground without rotating or cutting. It can gather soil samples with minimal disturbance, preserving the integrity of the soil layers for accurate analysis.
This technique is fast and efficient in soft to medium soils and is especially useful for temporary or exploratory projects. However, it is unsuitable for deep drilling or dense, rocky conditions, where rotary or percussion drilling would be more effective.
Core Drilling
Core drilling is a specialized technique for extracting cylindrical core samples from rock or other hard materials. It uses a hollow drill bit with a diamond- or carbide-encrusted edge to cut through the material, leaving a solid core inside.
Core samples provide geologists and engineers with detailed information about subsurface conditions. Core drilling is essential in the mining industry, where accurate knowledge of rock layers is critical for resource extraction.
Why You Need To Choose the Right Drilling Technique
Your choice of drilling technique directly impacts the quality of the investigation and the project’s safety. Each method has its strengths and limitations; for example, rotary drilling offers the depth required for large projects, while auger drilling provides fast and accurate samples for shallower tests.
Using the wrong technique could result in incomplete or inaccurate data, leading to costly delays or unsafe construction. Ensuring the right match between the technique and the site conditions saves time and resources.
The Importance of Geotechnical Drilling in Foundation Work
Foundation stability is critical to the success of any construction project. Geotechnical drilling helps determine the soil’s load-bearing capacity, the presence of groundwater, and the depth to solid bedrock.
Without proper geotechnical investigations, foundations may settle unevenly, leading to cracks, structural failure, or collapse. Conducting thorough soil tests ensures that the foundation will remain stable, protecting both the structure and its occupants.
Geotechnical Drilling Safety Measures
Safety is a top priority in any geotechnical drilling project. Proper planning, site preparation, and equipment maintenance are key to preventing accidents and ensuring the crew’s well-being. Here are some common safety precautions to follow:
- Complete pre-drill surveys: Conduct thorough site investigations to identify underground utilities, unstable soil, or hazardous materials before drilling.
- Provide protective gear: Ensure workers wear proper protective equipment, including helmets, gloves, and steel-toed boots.
- Perform equipment inspections: Regularly inspect tools and machinery for wear and tear to decrease the risk of accidents.
- Provide training and supervision: Make sure only qualified personnel operate the drilling equipment. Providing proper training and oversight will ensure safe operations.
- Establish emergency protocols: Set clear procedures for addressing equipment failure or hazardous conditions, and ensure all workers know these protocols.
Get Started With the Right Drilling Tools
At Jeffrey Machine, we understand the importance of having reliable tools for geotechnical drilling. We manufacture high-quality drilling tools, from augers to specialized drill bits, that will meet the demands of every project. We take pride in producing our tools in-house, ensuring the highest standards of quality and precision.
When you’re dealing with challenging ground conditions or deep drilling requirements, trust us to provide the right tools for the job. Our focus on innovation and durability allows us to help our customers achieve successful results.