How To Choose a Kelly Bar for Your Drilling Rig
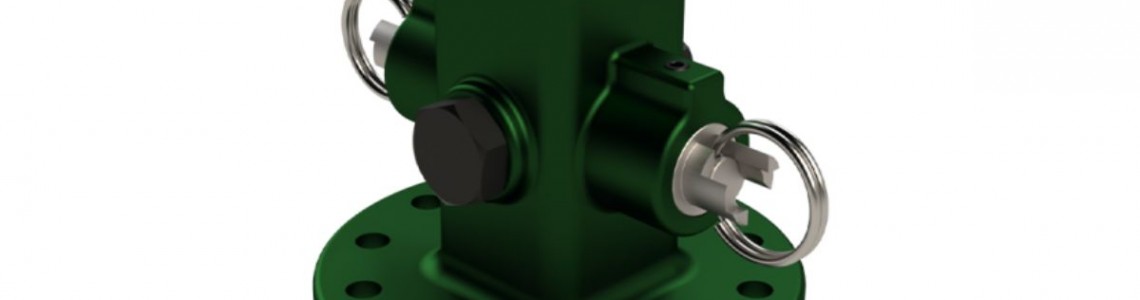
Selecting the right Kelly bar improves drilling efficiency, prevents unnecessary wear, and maximizes performance. This component is essential for deep foundation and piling projects as it transfers torque from the rotary drive to the drilling tool.
Choosing the correct type, size, and material affects drilling speed, stability, and overall job site productivity. Businesses must consider multiple factors when selecting a Kelly bar that fits their drilling rig and operating conditions.
Understanding the Role of a Kelly Bar
To choose a Kelly bar for your drilling rig, start by understanding its function in rotary drilling. This telescopic component extends and retracts during drilling operations, transferring torque and downward force from the rig to the drilling tool. The type of Kelly bar used directly impacts drilling depth, stability, and efficiency.
Kelly bars come in two primary designs: friction and interlocking. Each type serves specific drilling conditions and requirements. Selecting the appropriate type depends on soil consistency, drilling depth, and the rig’s torque capacity.
How Kelly Bars Affect Drilling Performance
The right Kelly bar improves torque transmission, allowing the drilling tool to penetrate soil or rock more effectively. A poorly matched Kelly bar can reduce drilling speed, create instability, and cause excessive wear on the rig. Selecting the correct design optimizes power delivery and extends the lifespan of the drilling equipment.
Different drilling environments require specific Kelly bar configurations. Hard rock and dense soil require interlocking Kelly bars for stronger torque transmission, while softer ground allows for friction Kelly bars. Matching the Kelly bar type to the drilling conditions prevents equipment strain and performance issues.
Comparing Friction and Interlocking Kelly Bars
Friction Kelly bars rely on continuous friction between telescoping sections to transfer torque. These bars work best in soft to medium-density soil conditions where high torque resistance is not required. They provide smooth operation and quicker drilling in less demanding environments.
Interlocking Kelly bars use mechanical locks to provide stronger torque transmission. These bars perform well in harder ground conditions, including rock and compact soil. The locking mechanism allows the Kelly bar to transfer higher torque loads, making it the preferred choice for deep foundation work.
Key Factors For Selecting a Kelly Bar
Several factors impact drilling efficiency and longevity when choosing a Kelly bar for your drilling rig. Selecting the right specifications based on drilling conditions and rig compatibility prevents mechanical failures and operational delays. A properly matched Kelly bar enhances jobsite performance and reduces unnecessary downtime.
The rig’s torque output, Kelly bar length, and drilling depth all affect performance. Choosing an incompatible Kelly bar can strain equipment, increase operational costs, and lead to premature component failure. Proper selection optimizes drilling output and minimizes wear.
Choosing the Right Length and Diameter
Kelly bars come in various lengths and diameters to accommodate different drilling requirements. Longer Kelly bars allow for deeper drilling, making them ideal for large-scale foundation work. However, using an excessively long Kelly bar on a low-torque rig reduces efficiency and may lead to operational instability.
Diameter impacts the strength and torque capacity of a Kelly bar. Larger diameters provide greater structural integrity and torque transmission. Selecting the correct diameter prevents bending or breakage under high-load conditions, maintaining stability during drilling operations.
Material and Durability Considerations
Kelly bars are typically constructed from high-strength steel to withstand repeated stress and torque loads. Standard steel bars provide durability for general applications, while reinforced designs offer additional resistance against extreme conditions. Businesses drilling in abrasive environments benefit from heavy-duty Kelly bars with enhanced wear resistance.
Protective coatings and specialized treatments improve corrosion resistance and extend the lifespan of a Kelly bar. Coated surfaces reduce friction, minimizing heat buildup and structural fatigue. Selecting a well-treated Kelly bar lowers maintenance costs and increases operational efficiency.
Balancing Cost and Performance in Kelly Bar Selection
Selecting a Kelly bar requires balancing cost with long-term performance. Lower-cost options may appear appealing but can result in higher maintenance expenses and reduced efficiency. Investing in a high-quality Kelly bar saves money over time by reducing equipment wear and minimizing operational downtime.
Businesses must evaluate their drilling needs before prioritizing budget over durability. A well-built Kelly bar reduces long-term expenses by maintaining performance and preventing frequent replacements. High-performance materials and precision engineering contribute to a more reliable and cost-effective drilling process.
The Trade-Off Between Price and Quality
Budget-friendly Kelly bars often use lower-grade steel and lack reinforcement. These bars may work for light-duty applications but wear out quickly under demanding conditions. Frequent replacements increase operational costs and disrupt jobsite productivity.
Higher-quality Kelly bars provide better longevity and resistance to extreme drilling conditions. The additional investment leads to fewer breakdowns, reduced downtime, and more consistent drilling performance. Choosing a superior product enhances efficiency while lowering overall costs.
Understanding Manufacturer Specifications and Warranties
Manufacturers provide specifications detailing torque limits, material composition, and structural reinforcements. Reviewing these details helps businesses select a Kelly bar that meets their drilling needs. A well-documented product provides insights into expected performance and durability.
Warranty coverage reflects a manufacturer’s confidence in its product. Companies offering extended warranties typically use higher-quality materials and advanced manufacturing processes. Selecting a Kelly bar from a reputable manufacturer increases reliability and long-term value.
Finding High-Quality Kelly Bars for Industrial Drilling
Choosing a reliable supplier ensures access to high-quality Kelly bars tailored to specific drilling conditions. Working with an experienced manufacturer reduces the risk of purchasing low-quality equipment that fails under pressure. A trusted supplier provides valuable guidance on selecting the best Kelly bar for each project.
At Jeffrey Machine, Inc. we provide high-performance Kelly bars and industrial drilling equipment designed for demanding applications. If your operation requires durable components, we offer Kelly bar adapters that improve compatibility and efficiency. Our team helps businesses select the right Kelly bar to maximize drilling performance and extend equipment lifespan.
The Importance of Customization in Kelly Bars
Custom Kelly bars improve efficiency by matching exact drilling requirements. Standard options may not always align with unique drilling conditions and require customization. Businesses operating in extreme environments benefit from tailored solutions that enhance performance.
Modifications such as adjustable torque limits, reinforced sections, and specialized coatings optimize drilling output. Customization prevents equipment strain and maximizes productivity in challenging drilling conditions. A supplier offering tailored options helps businesses achieve the best results.
Working With a Trusted Supplier
Experienced suppliers provide industry expertise and high-quality manufacturing standards. Businesses working with a reliable manufacturer gain access to better materials, precision engineering, and expert recommendations. A trusted supplier improves operational success by offering well-designed and durable Kelly bars.
Purchasing from an established manufacturer reduces the risks associated with poorly constructed drilling equipment. High-quality components minimize unexpected failures and maintenance costs. Working with professionals enhances long-term drilling efficiency and reliability.
A well-informed selection process leads to cost-effective and efficient drilling operations. Businesses should prioritize performance and durability when investing in Kelly bars. Work with Jeffrey Machine, Inc. today to find trusted industrial drilling solutions for your next project.