JEFFREY MACHINE MANUFACTURES NEW TOOLS TO TACKLE BIG JOBS
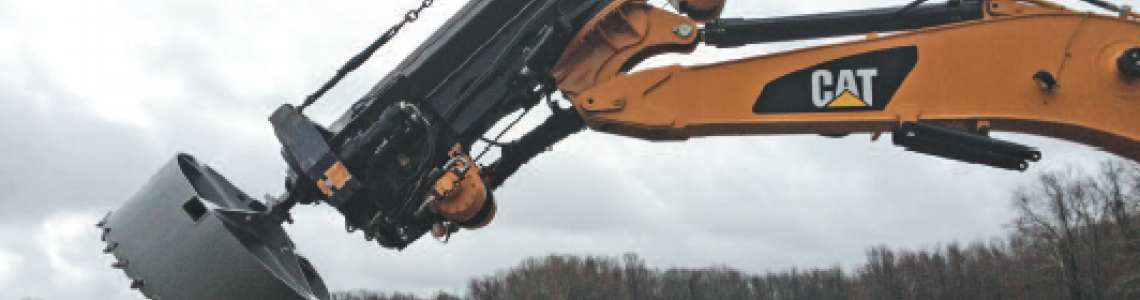
The following article first appeared in the February 2013 issue of Foundation Drilling and is used here with permission.
The following comes to us from ADSC Associate Member, Jeffrey Machine, Birmingham, Alabama. It is part of an ongoing series of articles that focus on the new developments in equipment and materials in the industries served by the ADSC. Members of the ADSC’s Associate Committee provide this information. Foundation Drilling magazine greatly appreciates the support it receives from the ADSC’s Associate Members. (Editor)
ADSC Associate Member Jeffrey Machine of Birmingham, Alabama has recently acquired a new state-of-the-art rolling press. They report it has cut lead times virtually in half for customers needing core barrels, clean-out buckets, drilling buckets, etc. Jeffrey imported a custom designed press from Europe and installed it at their location in November 2012. The press provides advanced capabilities and was recently put to the test.
THE NEED
ADSC Contractor Member, Cajun Deep Foundations, LLC of Baton Rouge, Louisiana needed a core barrel fast and called the auger manufacturer. They had an immediate need for a 72” core barrel and needed something that would cut through hard rock as fast as possible.
THE SITUATION
Cajun was one of several companies contracted to install a new transmission line for a power utility between two substations in Arkansas. Cajun’s part of the project was to construct drilled shafts for the large steel power poles. The depth requirement for the holes went as deep as twenty-eight feet and up to eight feet in diameter. Soil reports indicated that it was a moderate to hard shale type material. According to Gene Landry, Cajun’s Superintendent, “We brought tooling up here to drill through the soils that were indicated on the soil report provided to us.” He continued, “We were here in August and did another six shafts for them on the other side of I-30. Some places they said it was going to be hard and we had no trouble drilling it.” He explained that they were equipped with the same tools they had used successfully on that project. They are using a Cat excavator with a Watson EDT-7 attachment rated for 60,000 lbs. of rotary torque. The augers from various manufacturers are equipped with what Gene described as bear claw style carbide flat teeth.
THE PROBLEM
Commenting on the previous job Landry added, “It may have been hard (on some holes) but it was fractured so we could break it up pretty easily and retrieve it, but this stuff – we can’t find a seam in it.” They had drilled down eighteen feet in the problem shaft when their tooling ceased to make any progress. The requirements specified a twenty-six foot depth.
THE SOLUTION
The crew decided the best way to break through the impasse would be to use a core barrel to cut a ring around the outside di-ameter of the hole. This is a commonly used method that enables the resultant solid rock core to be broken up and removed. That’s when Landry called Jef-frey Machine and described their sit-uation. Timing was critical so the factory rep suggested they use the new .990 Dragon’s Tooth cutters for maximum speed. Gene commented, “I had the opportunity to use that Dragon Tooth – the old style – in 2006. They worked pretty well. The problem was if you dropped the tool too fast and it hit the bottom they would break.” Due to an undersized shank the breakage would occur at that point. He continued, “That’s what I talked to Tracy at Jeffrey Ma-chine about when we were building this one and he said they had changed the style.” Tracy told him that the larger diameter shank is better suited for the larger augers and higher pressures and assured him it would hold up to the task.
Only six days after taking Cajun’s phone call, Jeffrey’s Tracy Phifer arrived at the staging area in Arkansas with the newly made Dragon’s Tooth Core Barrel loaded on the company truck. It was the end of the day and it was pouring rain when he arrived but the crew came out to check out the new drilling tool. It looked aggressive but they would have to wait until the following day to put it to the test.
On site the following day everything was wet, mucky, and muddy. The excavator was fitted with the new core barrel, but hundreds of gallons of water would first have to be removed from the hole before they could start. It was several hours into the day before the new six foot diameter, thirty inch tall drill tool was lowered into the shaft. Once in position the operator started rotating the auger, adjusting torque and pressure. It cut fast. Within fifteen to twenty minutes it cut a two foot deep ring around the solid rock. When it bottomed out on the core bar-rel’s cross member it was removed from the hole and switched out for other tools to break up and remove the core. Tracy commented live from the job site, “As he’s drilling, water is seeping down the side wall of the can.” Needless to say, this was one of those messy jobs that aren’t much fun for anyone, but the impasse was overcome with the new drilling tool that Jeffrey Machine was able to pro-vide on such short notice. The tooth performed just as Tracy said it would. Also, at the end of the day, the teeth were all intact.
So to return for a moment to the rolling press, Jeffrey Sager, (the President of Jeffrey Machine), said the press can roll a two-inch thick slab of steel into a barrel as tall as ten feet high very quickly. Diameters on their current setup can be as small as two feet up to thirteen feet or more. This writer doesn’t have a clue how you could ship something that large but regardless, they can now produce it. Steel thicker than two inches can be used on shorter barrels. Jeffrey just finished a project making some four inch tall rings that were four inches thick.
Although the custom made press was a serious investment it greatly improves the factory’s ability to be more responsive to customers’ needs. While conventional business wisdom in this past year has caused many companies to downsize and pull back, Jeffrey Machine has chosen instead to buck the trend and expand their service edge. The new machinery adds some new capabilities adding new areas of potential growth into new markets.