JEFFREY MACHINE DRAGON TOOTH
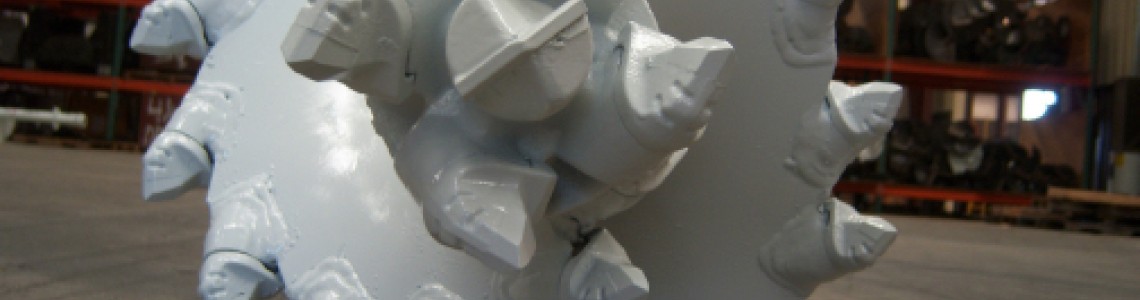
The following article appeared in the August 2013 issue of New Construction Products and is used here with permission.
Okay, so you have a job that requires boring holes for some utility poles. Tight timeframe, but you’ve got a good team and good equipment. The day’s going well, you’ve got three holes drilled already and the auger’s spinning on the fourth when it hits something hard and won’t go any further. Hard rock. Pull it out, unbolt the dirt teeth from your bolt on auger, bolt on the rock teeth and rock pilot. An hour later and maybe two inches deeper and the day’s not looking quite as happy. Okay, so pull it out and try the bullet auger. Nada. No better. What do you do at this point? You can bring in a bigger machine with a pressure rock auger, but even it might not work on what you’ve run into. Other options would be to bring in a trackhoe with a rock breaker followed by a vacuum truck like they commonly use in Canada. Your mind sees the visual of dollars flying into the sky. What do you do? Doesn’t anyone have a cost effective solution?
This is a type of scenario that happens frequently throughout the world. Fortunately, Jeffrey Machine, based out of Birmingham, Alabama has developed something that provides contractors with an extra edge against rock. The idea came from one of their customers. They work closely with contractors and one of them asked Jeffrey Machine to hard weld some non-rotating shark’s teeth into a tool for them. It was something they were using in the mining industry and it was doing a bang up job cutting rock. Jeffrey Machine built the tool and sure enough, it tore up the rock. Bad thing was that when the tooth wore out it had to be cut out and re-welded. This set Jeffrey Machine to the task of trying to recreate that non-rotating tooth so it would fit in a standard bullet tooth holder to allow for easy tooth replacement when necessary.
Took several years, but they finally created the Dragon’s Tooth. Although it uses the same size round shank as a standard bullet tooth, it does require a proprietary holder. The holder will accept a Dragon Tooth or a standard bullet.
Effective? You bet. In one instance, it cut 2500% faster than bullet teeth that were being chewed up by the bucketfuls. No significant wear on the Dragons either. In another case a contractor has cut over 1400 holes and the teeth are still going strong.
So, how’s it work? Well, a bullet tooth has a small piece of really hard carbide in the tip of this bullet shaped tooth. It’s made to rotate in the round holder as the auger turns. This is supposed to keep the tooth from wearing out on one side. It works kind of like a pencil sharpener and it’s been the standard rock cutting tooth for years. The Dragon doesn’t turn. Kind of hard to describe, but essentially it has a lip on the tooth that fits into a slot in the holder that keeps it from turning. It has a faceted surface and huge piece of sharp carbide along the cutting edge. All the wear is on the carbide and the carbide is harder than most rock. Because high grade carbide is very expensive, the tooth costs more up front, but typically costs less over the long haul. Additionally, because it cuts rock so much faster, there’s less wear and tear on the machinery and less money paying for workers to be standing around.
It’s available in .875 and .990 sizes.